What Strategies Ensure Product Quality With International Suppliers?
Navigating the complexities of international supply chains to maintain product quality is a challenge faced by many in leadership roles. From Co-Founders to CEOs, we've gathered five expert perspectives on how they ensure high standards across borders. Dive into insights starting with understanding product components and culminating with integrating technology for quality control.
- Understand Product Components
- Strategic Supplier Relationships
- Foster Continuous Improvement Culture
- Align Departments with Quality Standards
- Integrate Technology for Quality Control
Understand Product Components
We have a store that sells a variety of unique New Orleans ephemera. Keeping it local has been our focus, but we've recently branched out into wholesale for an international market.
And with that, we're sourcing supplies from all over the globe to keep up with increased demand.
The key through all of this is to understand where cost-cutting truly does not affect the end product. What are you doing custom that is perfectly OK to do in bulk? What parts of a product do not suffer from cheaper parts? Which do?
Understand your products down to the proverbial nuts and bolts (even if, like us, you don't actually have nuts and bolts in your product).
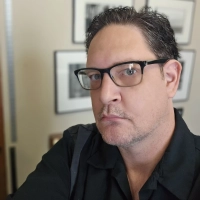
Strategic Supplier Relationships
The answer is simple: to keep an eye on the new developments in the market, to improve the quality of the material, and for this, we need to maintain a good, competitive, customer-focused, and strategic supplier base. The relationship with the supplier needs to be strategic rather than just buyer-seller.
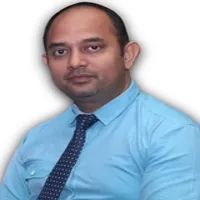
Foster Continuous Improvement Culture
Ensuring Excellence Across Borders
Maintaining product quality across international suppliers has been a strategic blend of clear communication, rigorous standards, and collaboration. First, establishing detailed quality specifications ensures suppliers understand expectations. Regular audits and inspections help monitor adherence to these standards. Additionally, fostering strong relationships built on trust and transparency encourages suppliers to prioritize quality. Utilizing technology for real-time monitoring and feedback enhances efficiency. Finally, fostering a culture of continuous improvement encourages suppliers to strive for excellence, ensuring consistent quality across all sources.
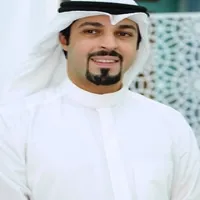
Align Departments with Quality Standards
In my experience, a significant challenge in maintaining product quality is ensuring consistent quality criteria across all areas and departments.
The reality is, when you're dealing with different international suppliers, product quality isn't solely the responsibility of the production team; it involves every department, from Human Resources to Logistics. If one area fails, it can negatively affect the performance of others. Even personnel hiring must align with quality control standards. The issue often arises when varying quality control criteria are in place, which can become problematic. Often, the rush and blind trust we place in our suppliers lead us to overlook failures in the raw materials, which can disrupt our workflow.
Integrate Technology for Quality Control
Keeping the product quality consistent between foreign suppliers calls for a complex strategy. Technology integration is one of the main tactics I've used to standardize quality inspections. Every one of our suppliers must utilize the bespoke app we created. This app allows them to submit real-time inspection data and guides them through our specific quality control procedures.
To ensure that every batch meets our color and quality criteria before shipping, an Indian textile supplier, for example, now submits photos directly through the app during the dyeing and cutting operations.
We cultivate our suppliers closely by involving them in the product development process. Suppliers who are involved proactively learn about our expectations and start their procedures appropriately. At our quarterly video-conference seminars, we investigate potential obstacles and exchange best practices throughout our supply chain.
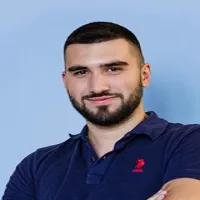